Nonwoven fabrics are characterized by their unique properties. They are ideally suited to technical applications and industrial use but also have an application in consumer goods. They are versatile, cost-effective, and recyclable materials that can solve a number of problems.
Nonwovens have a wide range of uses, from healthcare to agriculture. Especially in the medical sector, nonwovens are used for surgical masks, drapes, surgical gowns, sanitary pads, and more. These products have excellent barrier properties to protect skin from a variety of bacteria and viruses. Their strength, flexibility, and ability to absorb liquids make them an ideal choice for a variety of different industries.
While nonwovens have a wide variety of uses, they are most commonly used in disposable items. The low cost and durability of nonwovens are the main reasons why they are so popular. Compared to woven fabrics, they are also very flexible, breathable, and wrinkle-resistant. Depending on the nonwoven manufacturing process, the fabric can have a variety of thicknesses.
Nonwoven fabrics are manufactured by transforming fibers into loosely arranged networks through several processes. These include wet or dry laying, mechanically, chemically, or thermally. In wet laying, the fibers are suspended in water, which is then separated by specialized paper machines. A binder is then added to the paste, which is subsequently melted and added to the fibers. This results in an attractive, smooth, and durable fabric.
Mechanical processes involve the needling of short fibers, and adhesives are also used to bind the short fibers together. The mechanical processes are often used to achieve better drape and handleability, as well as to achieve the preferred orientation of the fibers.
Chemical and thermal processes can also be used to form nonwovens. For example, polypropylene is typically used to create nonwoven fabrics. During this process, polypropylene chips are bonded together to form a continuous filament. Polypropylene resin is a polymer that is non-absorbent and water-repellent. It also makes the fabric fluffy and pleasant to the touch.
In the most common manufacturing method, the nonwoven fabric is created by forming a fibrous web from small fibers. The fibrous webs are then consolidated using various techniques. There are three main methods: needle punching, thermal binding, and air laying. Each technique is capable of achieving the desired fiber orientation. However, all of these methods are only suitable for thin, lightweight fabrics, and aren't suited for heavier-weight or long-lasting products.
Because of their durability, nonwovens are also used for industrial and automotive applications. Unlike woven fabrics, they don't require fiber conversion into yarn, so they can be reused and recycled. They are also wrinkle-resistant and can resist high temperatures.
The main function of 3D nonwovens is to provide insulation. To achieve this, the fibers are oriented in a shaped shell structure. Normally, the thickness of the nonwovens is several hundred times the diameter of the fibers.
Traditionally, nonwovens have been used in medical applications, but they have recently been applied in several other fields as well. Examples of these include surgical drapes, surgical gowns, sanitary masks, and tissue scaffolds.
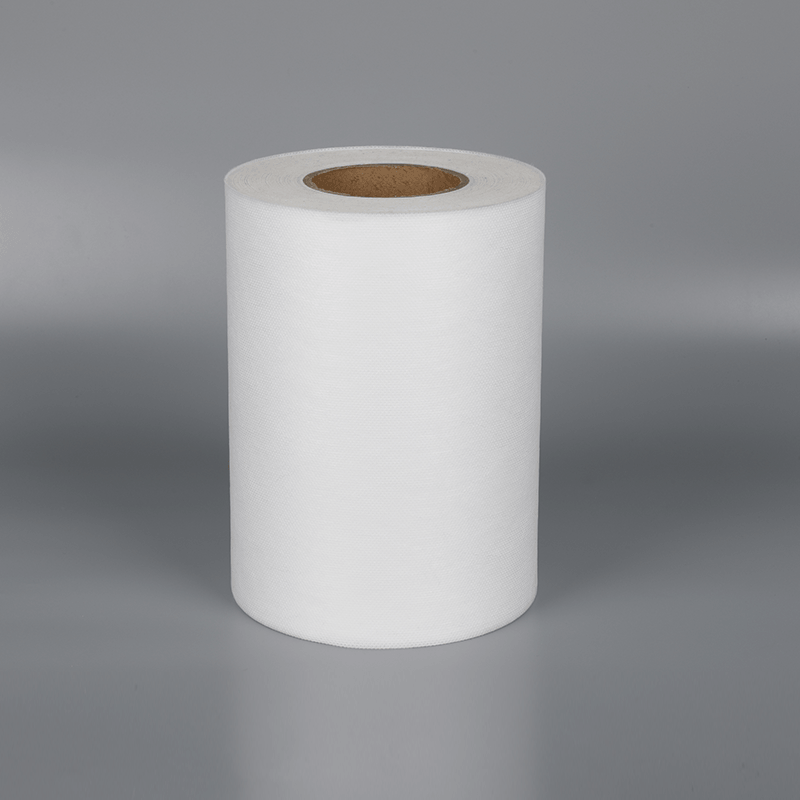
Bi-component nonwoven fabric
Weight |
10gsm -100gsm |
Width |
Max 1.6m |
Color |
According to customer’s request |
Capacity |
10 tons/day |